Nothing's in my cart
<< Back to Stories
XR Training Makes Forklift Operators Safer
How Virtual Forklift leveraged HTC VIVE Focus 3 technology to transform forklift training throughout the logistics industry.
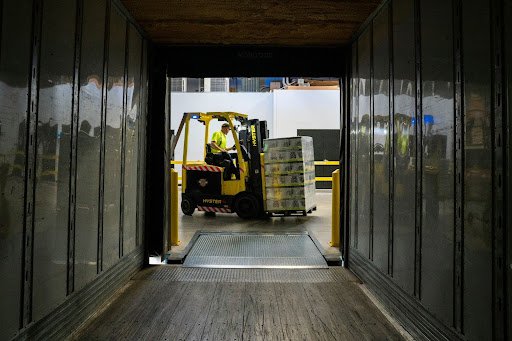
Manufacturing | Training/Simulation | Case Study
6 minute read
Forklifts are the backbone of the modern economy. Without them, global logistics processes grind to a halt.
They’re also heavy, dangerous machines. According to OSHA estimates , forklift accidents lead to 35,000 serious injuries and an additional 62,000 non-life-threatening injuries every year. Skills and safety training is one of the top priorities for any industry that relies on forklifts — yet for many companies operating within the United States, these training processes amount to little more than a video and a test before putting operators in dangerous situations.
Virtual Forklift (1) addresses this information gap head-on with a powerful and immersive simulation program. Created by current and former forklift trainers, Virtual Forklift provides the knowledge and training tools to keep operators safe while ensuring consistent outcomes that employers can trust.
The Challenge
The average forklift weighs around 10,000 pounds. Many rely on rear-wheel steering, which increases maneuverability in tight spaces and improves weight distribution but requires a vastly different set of driving skills than standard front-wheel drive vehicles. Despite these obvious dangers, the United States has no standardized forklift certification process. Evaluation and certification are primarily left up to the employer.
In theory, this approach allows each organization to develop instructional processes that fit its specific needs. In practice, this leads to inconsistent training methods, an increase in potential OSHA safety violations, and a constant need to recertify whenever a forklift driver changes employers.
Improving forklift operator safety was a primary concern for Scott Peloso, Business Development Manager at Virtual Forklift, who was directly impacted by improper training. For him, safety isn’t just about operational efficiency; it’s about protecting the people who get the work done. Current training methods just weren’t cutting it.
“There’s no standardized certification that a forklift operator can use everywhere, which creates gaps for both employers and drivers,” Scott explains. “You can even get an online certification for as little as $100, but that doesn’t mean someone has the practical experience or knowledge to step onto a warehouse floor and operate a forklift safely.”
As a result, many employers struggle to find and retain qualified forklift operators. “One of the main problems with new hires, or even some people with experience, is that you can talk your way into getting on the floor because people want to believe you,” says Peloso. “It becomes a real problem when those people mess up on the floor, and the employer then has to take them aside and say, ‘Hey, it seems like you don’t have the skills you said you said you did.’”
These organizations (and the forklift training schools they might contract to provide instruction) needed a solution that could be customized to their specific needs, meet their state or region’s certification requirements, and impart valuable skills with verifiable metrics.
The Solution
Virtual Forklift saw a desperate need to fill this instructional gap and realized that an XR solution powered by HTC VIVE was the way to do it. Leaning on over 20 years of forklift training expertise, conversations with employers, and technology partnerships, Virtual Forklift devised several simulation products that could meet its clients’ instructional and budgetary requirements while imparting a consistent quality level of knowledge.
The company didn’t set out to completely replace hands-on training and operator evaluations. Instead, Virtual Forklift developed a supplement to live forklift training where new employees could safely learn a complex piece of machinery while experienced operators could practice new attachments and hone their skills.
In addition to its simulation accuracy and safety, Virtual Forklift modernizes the training experience, appealing to younger operators and digital natives who find the interactive modules more engaging and accessible than traditional methods.
Once trainees feel confident enough in their abilities in the virtual environment, they can then practice those skills on real hardware and take the required evaluation to move onto the floor.
“The primary advantage of XR training is its ability to simulate a highly realistic, risk-free environment, leading to faster, safer, and more effective training,” says Peloso. “Our modules not only meet OSHA compliance, they exceed it by adhering to safety standards in regions like the UK and Canada, which are more rigorous than those required by OSHA.”
On the software side, Virtual Forklift Nexus offers a wealth of driving drills and modules designed to teach critical operational skills and safety procedures. Trainees learn concepts like figure-8 and 90-degree turns, how to move pallets, and weight balance management. Virtual Forklift has also developed training modules to target the enhancement of specific skills, like dealing with forklift attachments, loading trucks, and even specialized racking. Students can repeat these modules as often as they’d like in order to refine their skills before transferring those skills to a live forklift.
Virtual Forklift delivers this software alongside a modular hardware solution that relies on HTC VIVE Focus 3 to deliver the most realistic forklift simulation ever designed. Virtual Forklift scales based on client needs, whether that’s a mobile control set-up for travel between training locations or larger stationary set-ups intended for integration into training rooms and classrooms. This scaling also transitions to other HTC VIVE hardware, like the powerful HTC VIVE XR Elite and the new HTC VIVE Focus Vision, to ensure flexibility and uniformity in hardware and deployment.
“Our XR training modules focus on critical forklift operation skills, including safe handling, maneuvering, load management, and precision in challenging scenarios like tight spaces,” Peloso says. “These modules are designed to build foundational skills for new operators and advanced competencies for experienced ones. This simulator and the associated training material address 90% of real-world scenarios at a worksite. We’re addressing the most talked about problems a company might experience during any given workday.”
In addition to offering standard, off-the-shelf modules, Virtual Forklift can be customized to suit client specifications. The Virtual Forklift team works directly with each organization’s logistics division to develop a virtual recreation of the layouts and conditions employees will interact with during the workday while mapping safety processes to internal requirements. They can then apply their customized software solution to an HTC VIVE headset that fits into their training pipeline, whether they prefer the portability of the VIVE XR Elite or the fidelity of the VIVE Focus 3. This customizability allows clients to select specific forklift training modules tailored to their precise needs.
Results
With Virtual Forklift, businesses no longer need to devote dedicated warehouse space or reduce productivity by pulling live forklifts off the floor for training. Instead, instructors can teach actionable skills in a safe, virtual environment anywhere they have available space — and the results have been staggering.
- Knowledge retention rates have shot up to nearly 80% with Virtual Forklift, compared to around 50% with traditional training methods.
- Rather than practicing new skills on real forklift hardware, students can train in an immersive, risk-free environment. As a result, Virtual Forklift observed a 100% reduction in training-related accidents when compared to live forklift training.
- Trainees have experienced a 65% reduction in the time required to learn essential forklift operation skills.
- Learner engagement rates jumped from 30% to 85%, enhancing skill retention and long-term proficiency.
In addition to these results, the ability to learn these critical skills in a stress-free environment gives training operators a chance to test out what they’ve learned with greater confidence.
“The HTC VIVE Focus 3 has transformed forklift training by moving from passive methods like reading and videos to immersive, hands-on VR experiences,” says Peloso. “This shift has increased retention rates while also boosting confidence as employees practice in a realistic, risk-free environment. The result is a more engaging, effective, and impactful learning experience that better prepares operators for real-world tasks.”
Virtual Forklift has also worked closely with other businesses and forklift schools to customize its training solution to meet their exacting requirements — like a recent project for Bowling Green Metalforming (2), a global automotive supplier in Kentucky with a 1.6 million square foot factory operating anywhere between 80 to 100 forklifts at a time.
“My contact at Bowling Green, Asherah Bosely, told me that the most common problem they have is employee retention,” Peloso explains. “Even the best operators were having a hard time on the floor because the facility is so massive and busy that it’s almost like dealing with legitimate road traffic. Trying to retain employees, trying to come up with better training, trying to reduce the total number of incidents — all of these posed significant problems.”
Together, the teams at Bowling Green and Virtual Forklift devised a process that would allow new employees to come on board, train within Virtual Forklift’s immersive representation of the Bowling Green Metalforming plant, get certified, and then go out on the floor. Along the way, Virtual Forklift gathered metrics to ensure that employees had the skills they needed to operate a forklift as safely as the best workers on the floor.
Through the combination of HTC VIVE Focus 3 hardware and Virtual Forklift’s customized training solution, Bowling Green Metalforming was able to train new and existing operators on the unique layout of its large-scale manufacturing plant more effectively than traditional methods. Not only did this solution reduce the total number of accidents on the floor, it allowed the company to retain top talent by improving operator confidence and reducing the potential for injury.
Once this pilot program is complete, Virtual Forklift plans to leverage HTC VIVE Focus 3 hardware to integrate the training and experiences learned at Bowling Green Metalforming to expand operations and roll out a nationwide training program — offering customized simulations coupled with the best XR technology on the market to boost knowledge retention and safety results on factory floors and logistics hubs across the country.
Why VIVE
When it came time to choose a headset to power the realistic and immersive training simulations Virtual Forklift’s clients need, HTC VIVE was the obvious choice.
“The realism and consistency of the HTC VIVE Focus 3 is just tops,” says Peloso. “Nothing else has met our needs and been as crisp and clean as that headset. It’s so good that we built one of our simulators with a roll cage on it, and when people turn around, they grab that back bar to help them look. It makes everything that we do better.”
HTC VIVE Focus 3 offers sharp 5K resolution imagery, a smooth 90hz refresh rate, and a 120-degree field of view, offering unparalleled clarity and immersion across Virtual Forklift’s mobile and stationary simulator configurations. HTC VIVE also provided direct, hands-on support to help Virtual Forklift make its product as successful as possible.
“The team at HTC VIVE has helped us as much as they could in every single aspect,” Peloso says. “They even flew out here to check out the simulator and offer feedback. I don’t know if every company would do that, but I know that they did.”
Virtual Forklift's partnership with HTC VIVE is more than just a vendor relationship — it’s the start of a safety and training revolution within the logistics industry.
“This isn’t just a shift in training,” Peloso says. “It’s a global transformation. We now have the ability to set up Virtual Forklift Driver Training Centers anywhere, without the need for a physical forklift or traditional training space, allowing us to bring this program to classrooms and businesses alike. Part of our mission is to revolutionize how forklift training has been done for the last 20+ years, and HTC VIVE’s XR technology has made those goals more realistic and achievable than ever.”
With this foundation in place, Virtual Forklift is ready to begin rolling out similar integrated solutions at plants in Kentucky and across the country through partnerships with SkillsUSA, the Kentucky Workforce Innovation Board, South Central Kentucky schools, and Bowling Green Metalforming's parent company Magna International.
Schools participating in this program will receive extensive, hands-on training through an integrated “train the trainer” course. Thanks to Virtual Forklift’s 20+ years of experience, this process will transform school staff into adept forklift trainers, and the program’s high standards and accessibility will allow this program to expand to schools everywhere. Soon, businesses will be able to partner with schools to offer customized forklift training programs that prepare future operators for well-paying jobs while maximizing their safety.
“Our pilot program, launching soon, bridges the gap between education and industry, preparing individuals for real-world employment opportunities,” Peloso says. “With key contributors like HTC VIVE and Bowling Green Metalforming, we’ve demonstrated how this can be a practical, viable solution for connecting schools with businesses that need skilled forklift operators. It’s not just about training anymore — it’s about real job creation and employment pathways.”
Contact VIVE
Would you like to discuss your virtual reality project with a member of the HTC VIVE team?
(1) Virtual Forklift, https://virtualforklift.com/
(2) Bowling Green Metalforming, Bowling Green Works, https://www.bowlinggreenworks.com/business/bowling-green-metalforming/